Mit Hilfe der Kettenanalyse werden für komplexe Baugruppen wie Werkzeugmaschinen die statischen und dynamischen Beiträge der einzelnen Komponenten und Unterbaugruppen simulativ und automatisiert ermittelt.
Geschichtlich ist die Kettenanalyse aus einem praktischen Problem heraus entstanden: Wenn nur Gesamtbaugruppen simuliert werden, dann ergeben sich die statischen und dynamischen Verformungen aus einem komplexen Zusammenspiel von gekoppelten, sich gegenseitig beeinflussenden Effekten.
Nehmen wir beispielsweise eine Schleifspindel. Diese kann man sich wie eine dicke Welle vorstellen, die in der Regel beidseitig durch Wälzlager reibungsarm und präzise gelagert wird. Wir beobachten bei den Schleifspindeln eine relevante Biegeschwingung. Nun könnte man diese Biegeschwingung auf zwei Arten verbessern: Entweder wird die Welle biegesteifer und/oder leichter oder die Lagerung torsionssteifer. Das ist ein Entweder/Oder-Ergebnis. Es reicht also, wenn eine von den zwei Maßnahmen umgesetzt wird, um eine deutliche Verbesserung zu erzielen.
Nehmen wir ein zweites Beispiel von einem Fahrständer. Das kann man sich wie eine turmartige Blechschweißkonstruktion vorstellen, die auf vier Führungswägen in einer Richtung rollen kann, das Ganze angetrieben durch einen Kugelgewindetrieb. Wir stellen fest, dass der Fahrständer eine Kippschwingung ausführt, bei der sowohl die Führungen als auch der Kugelgewindetrieb eine wichtige Rolle spielen. In diesem Fall reicht es nicht nur den Kugelgewindetrieb steifer zu machen. Und es reicht auch nicht nur steifere/größere Führungen einzubauen. Die zwei Elemente sind verkettet und müssen gleichzeitig verbessert werden, um das Gesamtergebnis deutlich zu beeinflussen.
Nun hat man in einer komplexen Baugruppe viele Komponenten und entsprechend hoch ist die Anzahl der möglichen "Stellschrauben". Die Frage stellt sich also, welche Stellschrauben am wichtigsten sind.
In der Vergangenheit haben wir versucht diese grundlegende Frage auf Basis von Simulationsergebnissen der Gesamtbaugruppe zu beantworten. Diese Vorgehensweise ist relativ zeitintensiv und interpretationsanfällig. Es ist nicht leicht bspw. relevante Schwingungen von unwichtigen Schwingungen zu trennen. Oft überlagert eine harmlose Blechschwingung eine wichtige Spindelschwingung. Außerdem ist die Ursachenkette für eine spezielle Schwingung nicht einsehbar. Und schließlich kann nicht gesagt werden, wieviel sich eine Schwingung ändert, wenn eine spezielle konstruktive Änderung vorgenommen wird, ohne dass man die komplette Baugruppe nach der Änderung noch mal simuliert. Das entspricht also zu stark einem Trial-and-Error-Ansatz, der allerdings zum Glück nicht mehr experimentell sondern simulativ stattfindet.
Mit der Zeit wurde der Wunsch nach einer standardisierten und automatisierten Auswertungsmethode immer lauter. Die Lösung wurde durch die so genannte Kettenanalyse herbeigeführt. Die Kettenanalyse ähnelt stark einem Zusammenbauen der Baugruppe. Man beginnt an einem Ende der Baugruppe und baut zunächst das allererste Bauteil oder die erste Einheit zusammen. Dann kommen die nächsten logischen Einheiten schrittweise hinzu, bis man die komplette Baugruppe zusammengebaut hat. Nach jedem Schritt wird eine komplette Simulation und Analyse durchgeführt. Es wird also nicht eine Simulation durchgeführt, sondern es werden typischerweise 12 Ausbaustufen der Baugruppe simuliert. Schließlich werden die Verformungen der einzelnen Stufen verglichen und die Differenzen gebildet. So erhält man am Ende eine präzise und vor allen quantitative Aussage über die Einflussfaktoren.
Durch intelligente Automatismen lassen sich alle Stufen mit wenig Aufwand (nicht mehr als bei einer einzigen Simulation) simulieren und auswerten.
Es können alle ausgewählten Stufen auf einmal berechnet werden und auch ist die Erstellung von Balkendiagrammen der Einflussfaktoren ist automatisch möglich.
In der Regel ist sowohl die statische als auch die dynamische Nachgiebigkeit einer Baugruppe interessant. Und oft stehen sich die zwei Ziele entgegen. Es kann also durchaus passieren, dass eine Verbesserung der statischen Steifigkeit zu einer Verschlechterung der dynamischen Steifigkeit führt. Wir müssen also beide Größen auswerten und im Auge behalten.
Anstatt, dass wir zwei Simulationen (eine statische und eine dynamische) durchführen, können wir den Aufwand deutlich reduzieren, wenn wir nur eine dynamische Simulation durchführen, denn die statische Nachgiebigkeit ist in der dynamischen bereits enthalten. Man kann die statische Nachgiebigkeit als eine dynamische Nachgiebigkeit aber bei tiefen Frequenzen sehen. Im Speziellen berechnen wir Nachgiebigkeitsfrequenzgänge und extrahieren daraus automatisch den statischen und dynamischen Anteil.
In den folgenden Animationen sind die unterschiedlichen Stufen einer Werkzeugmaschine zu sehen. Außerdem kann man in den Nachgiebigkeitsfrequenzgängen verfolgen, auf welche Art und vor Allem wie viel sich einzelne Resonanzen über die einzelnen Stufen verschieben. Die größten Einflüsse kann man schon mit dem bloßen Auge leicht erkennen. Das abschließende Balkendiagram kann man wie eine Art Fingerabdruck der Maschine sehen. Wenn alle einzelnen Bereich gleich lang wären, dann wäre die Konstruktion optimal. In der Praxis kann das Optimum jedoch nie 100%ig erreicht werden. Je größer die Unterschiede zwischen den einzelnen Balken, desto weiter ist die Maschine vom Optimum entfernt.
Stufen einer Werkzeugmaschine:
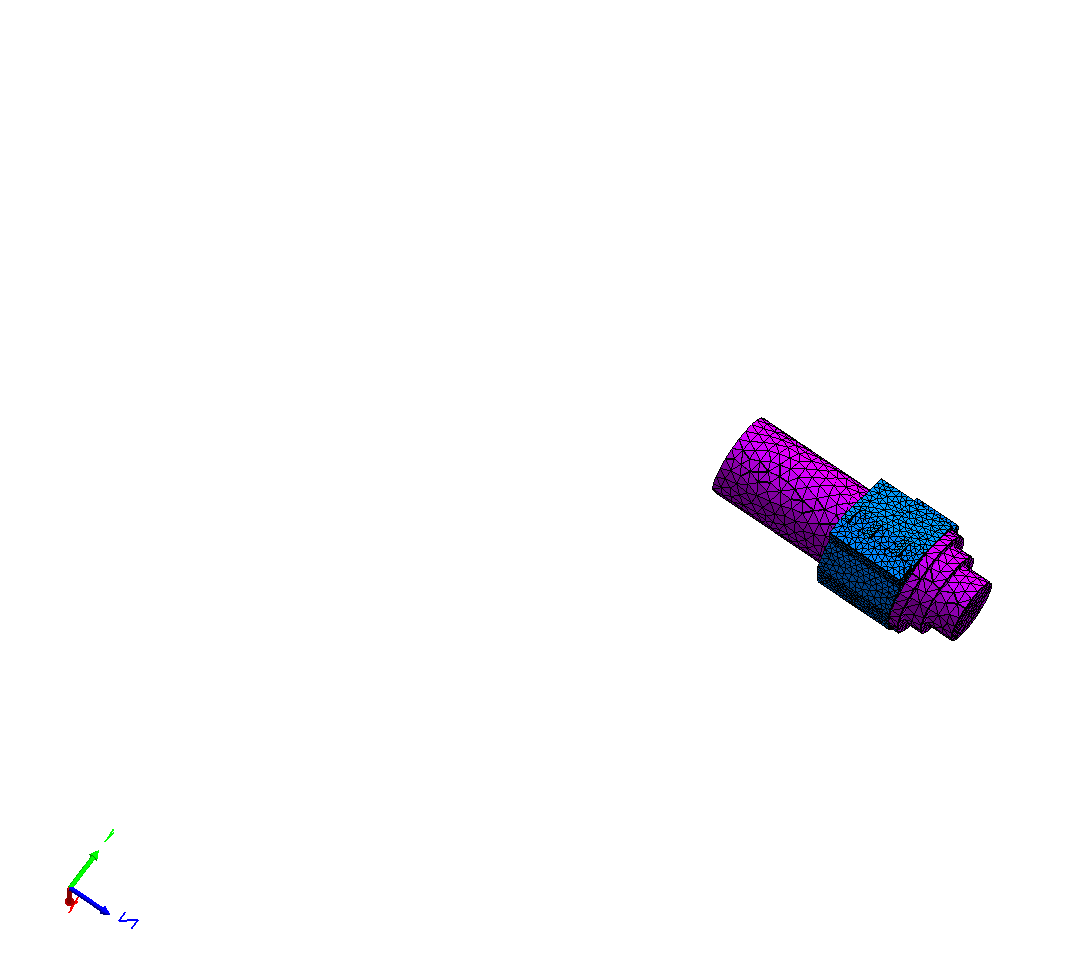
Veränderung der Resonanzen über die Stufen
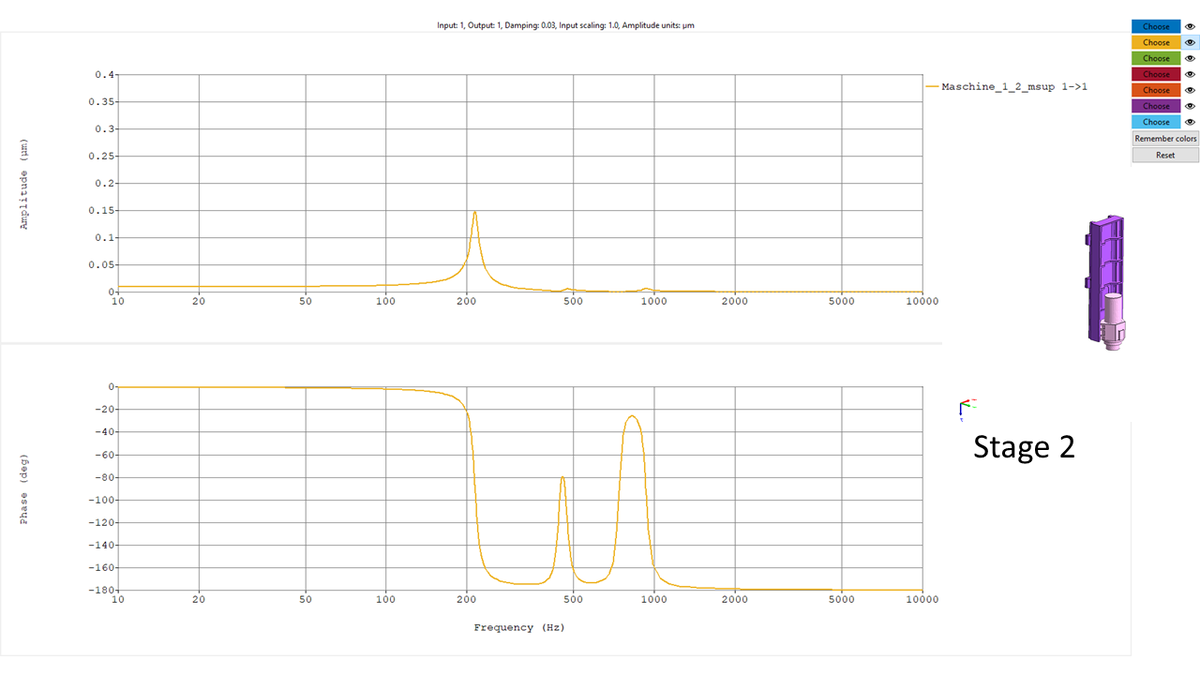
Balkendiagram als Fingerabdruck der Maschine
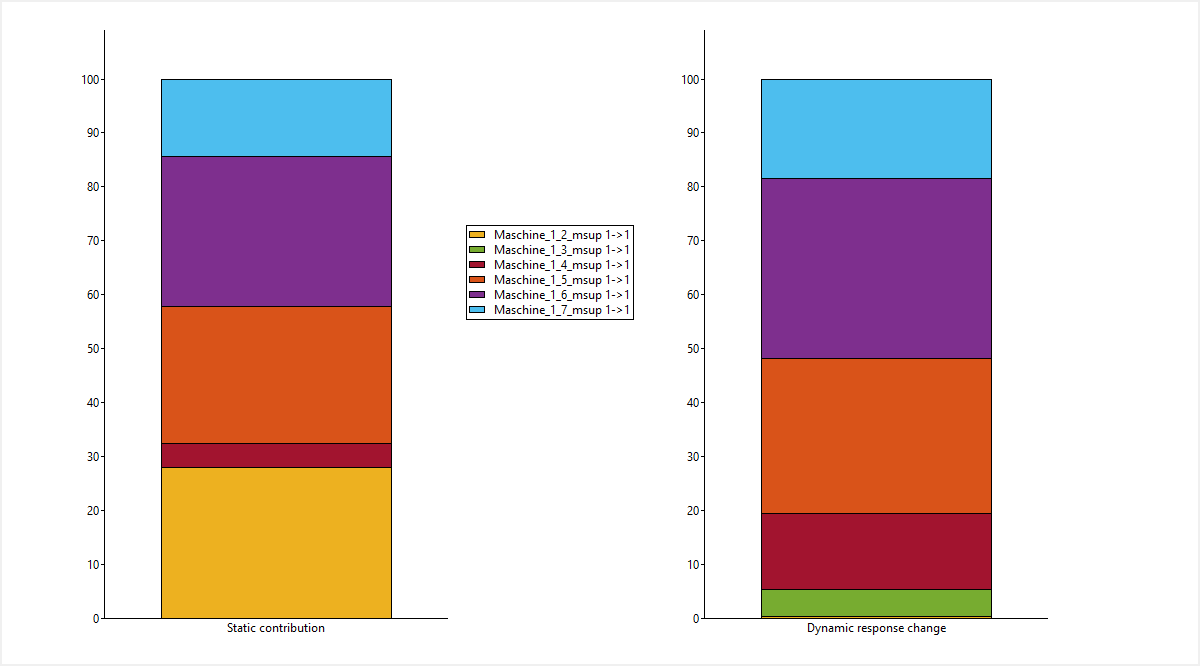